Noah
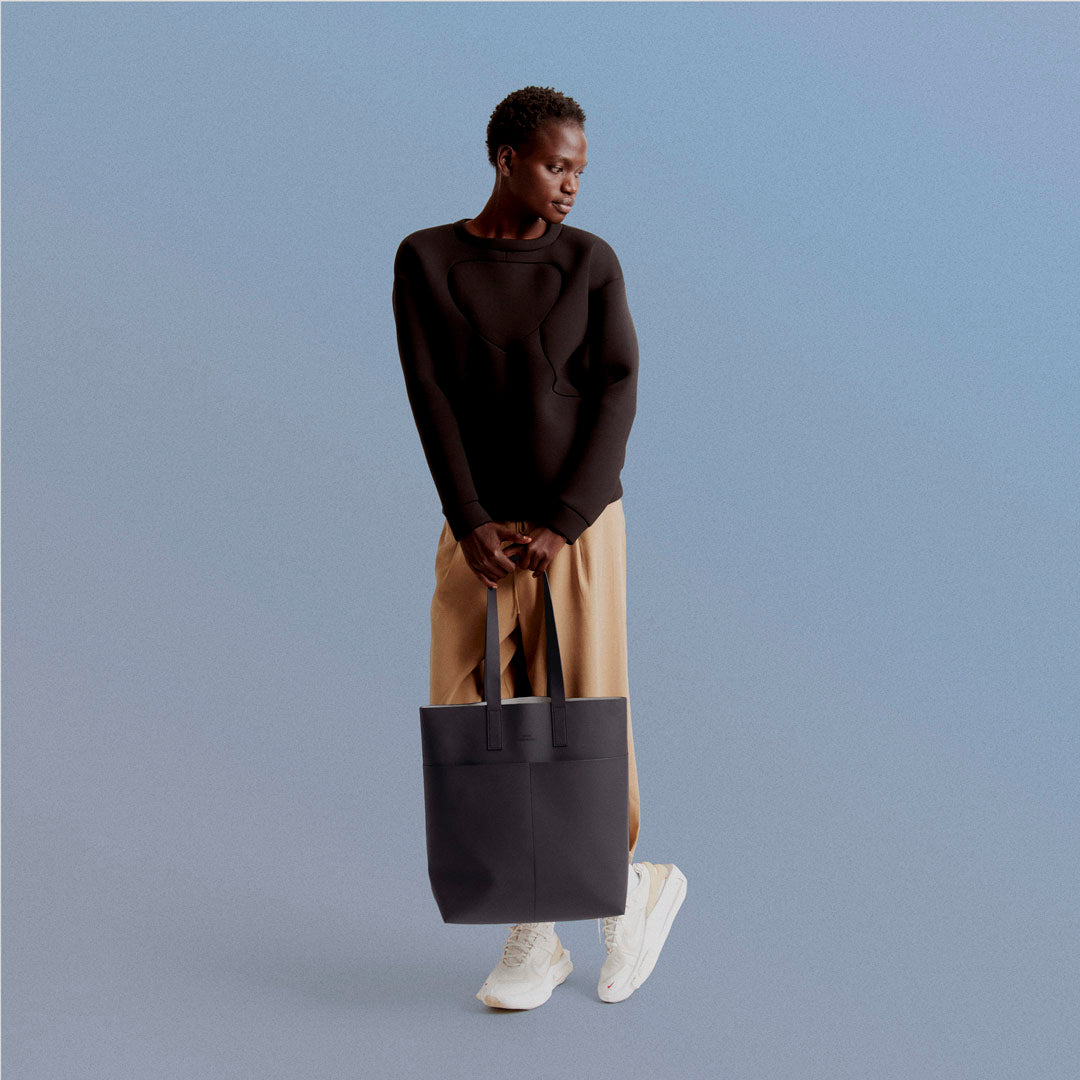
Taking life lightly
Ucon Acrobatics
Noah Bag
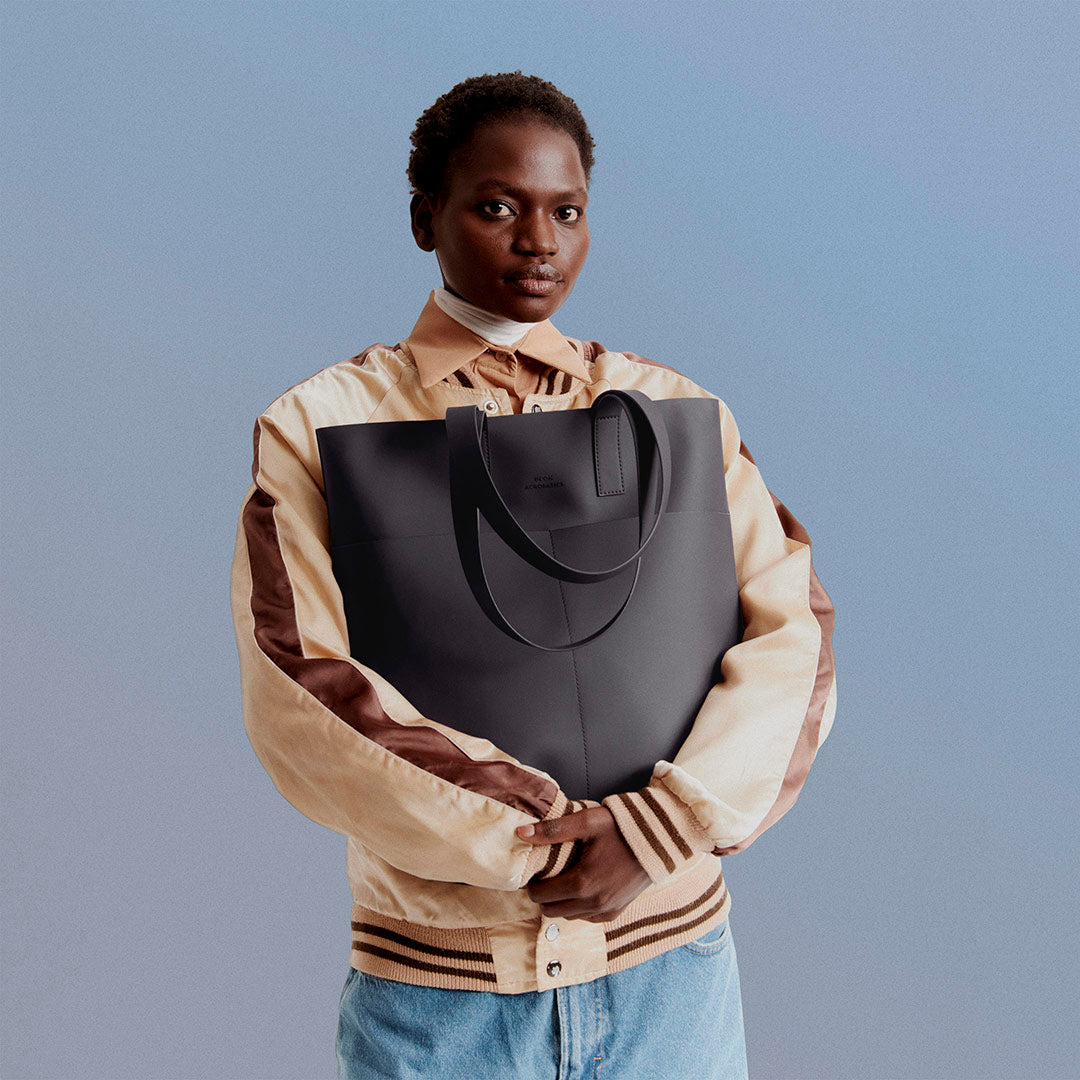
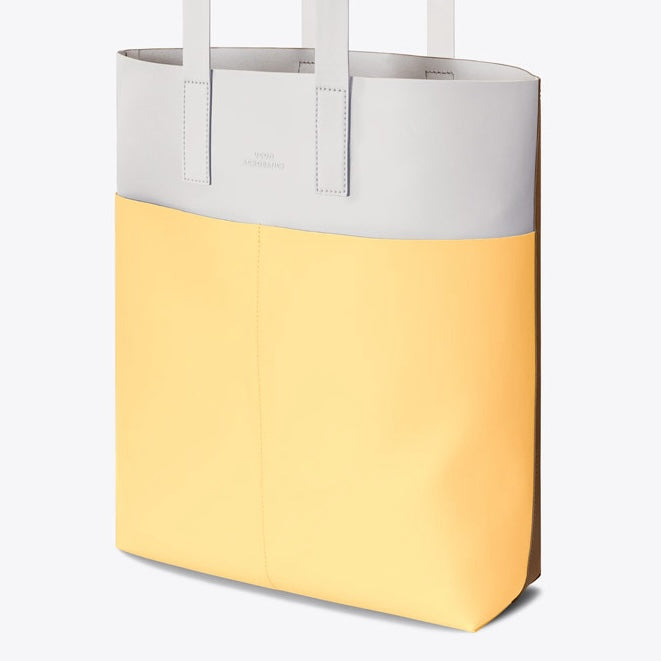
Lotus Infinity Series
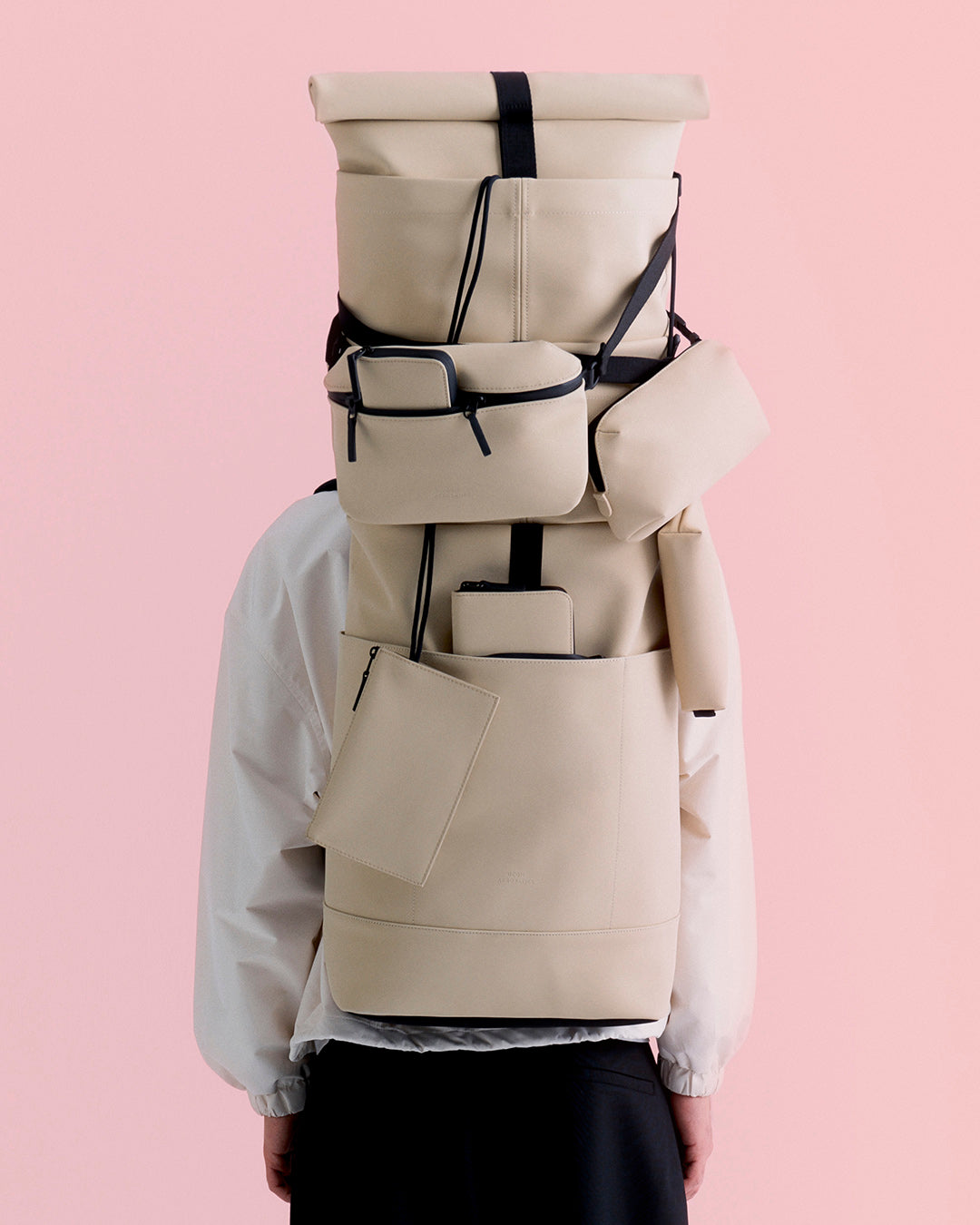
Ucon Acrobatics
Noah Bag

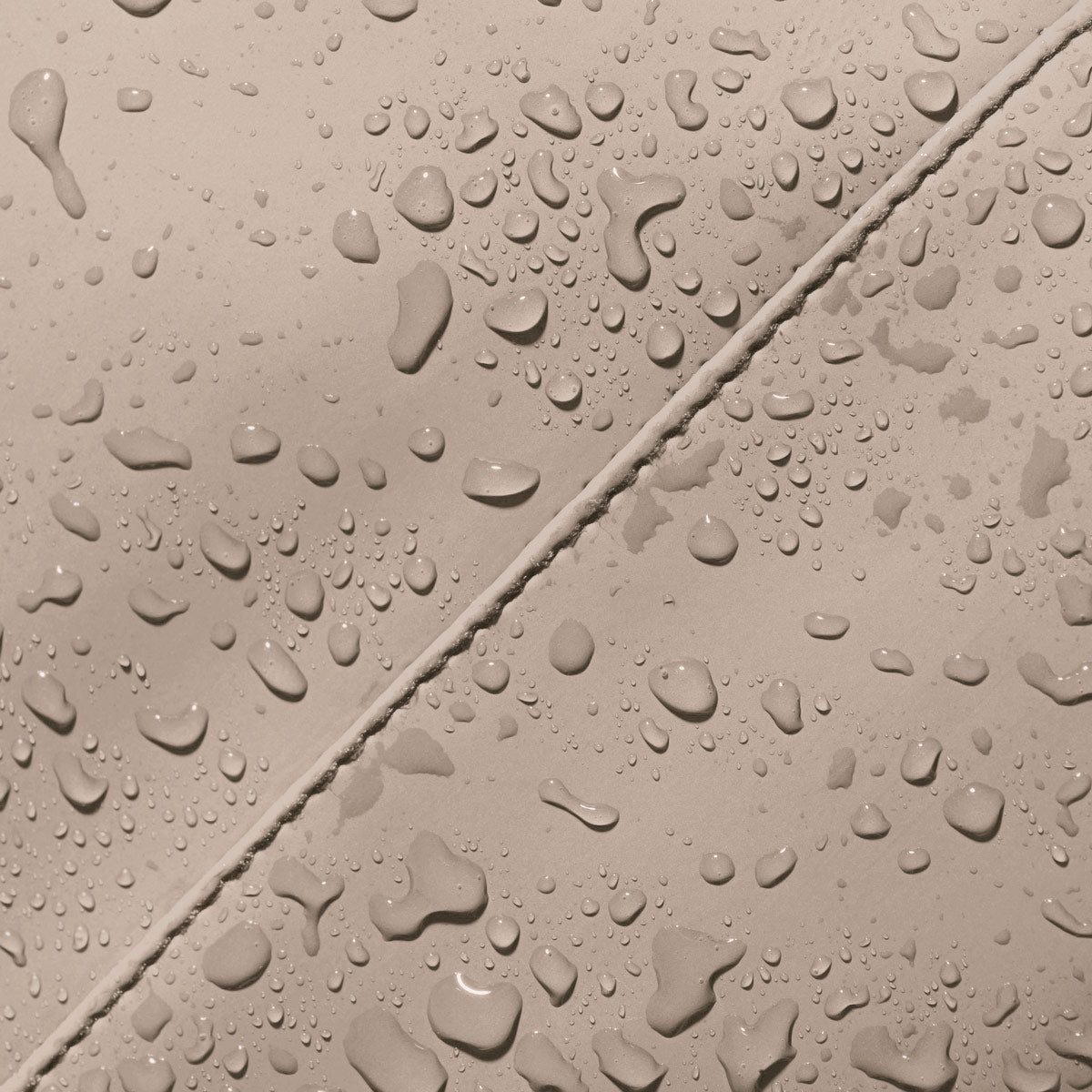

MINIMAL DESIGN
Our durable, timeless designs for urban nomads are the result of environmentally friendly and social decisions as well as passion and creativity.
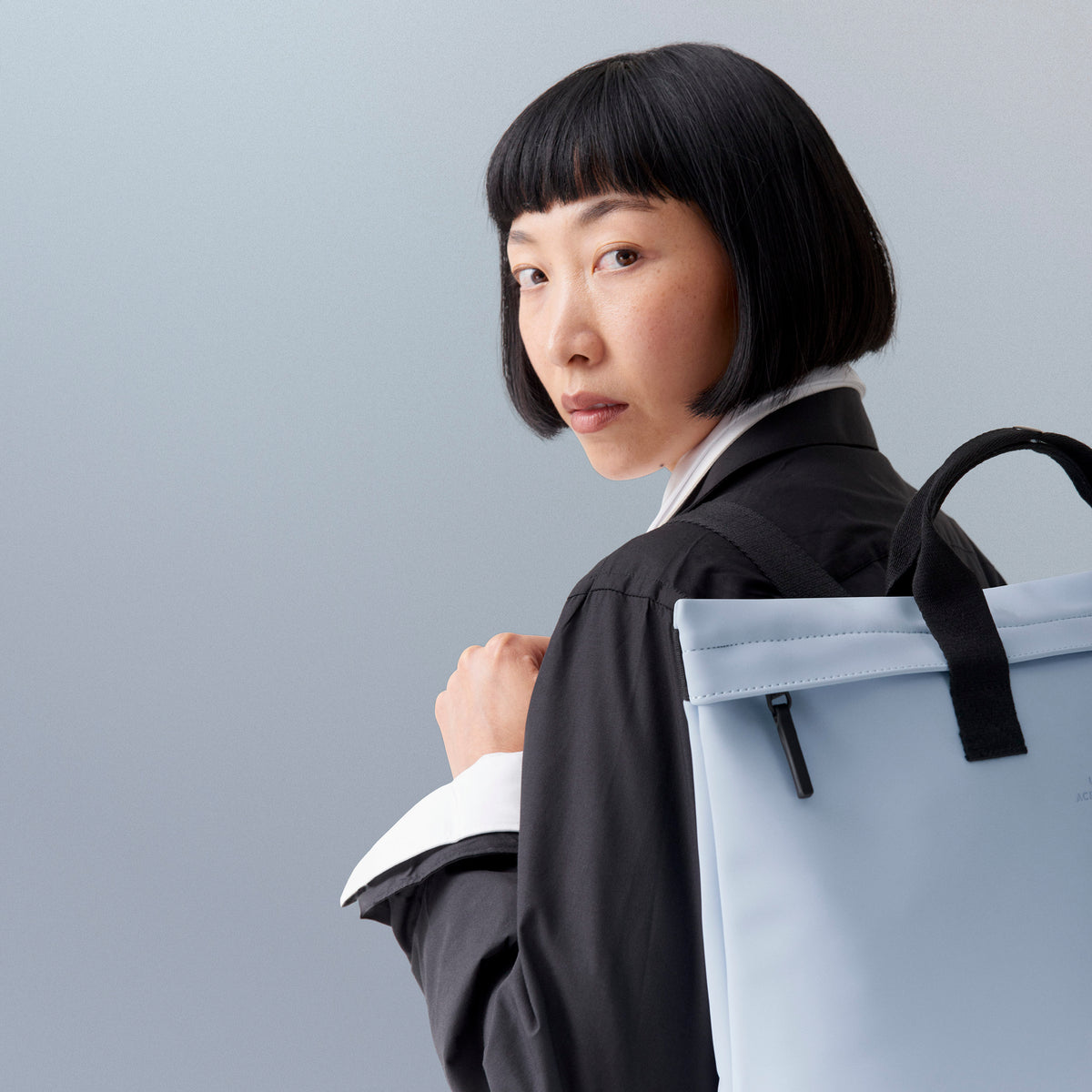
MINIMAL EMISSION
We want to create the best product possible without causing any unnecessary damage. For this plan to work and for us to be able to inspire and implement environmental solutions, we work with carefully selected associations and partners.
A Change in Material - A Change for the Climate
Here are the key innovations
Largest possible percentage of recycled textiles
Extended lifetime
Reduced ecological footprint
Designed for the circular economy
How would such a 'innovation' look like?
Sustainability doesn't always have to look 'eco'. In our case, you can hardly tell the difference. Often they are not visible, because we look where no one looks. Hard plastics and foams are hidden in every backpack sold today. We have found a way to avoid all of that and use textile waste instead.
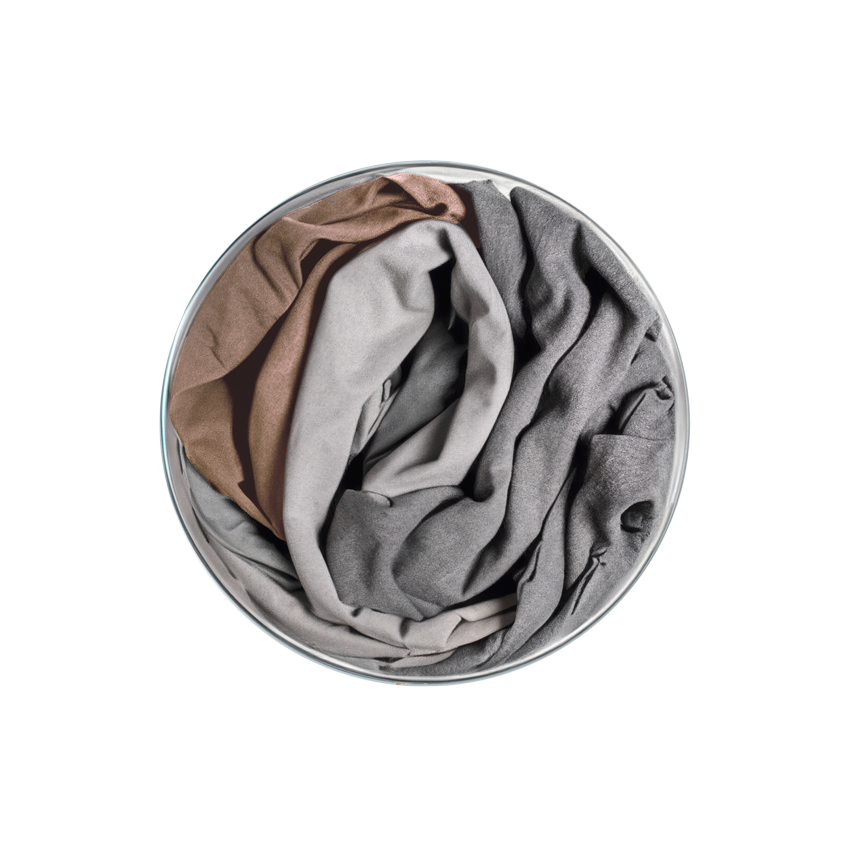
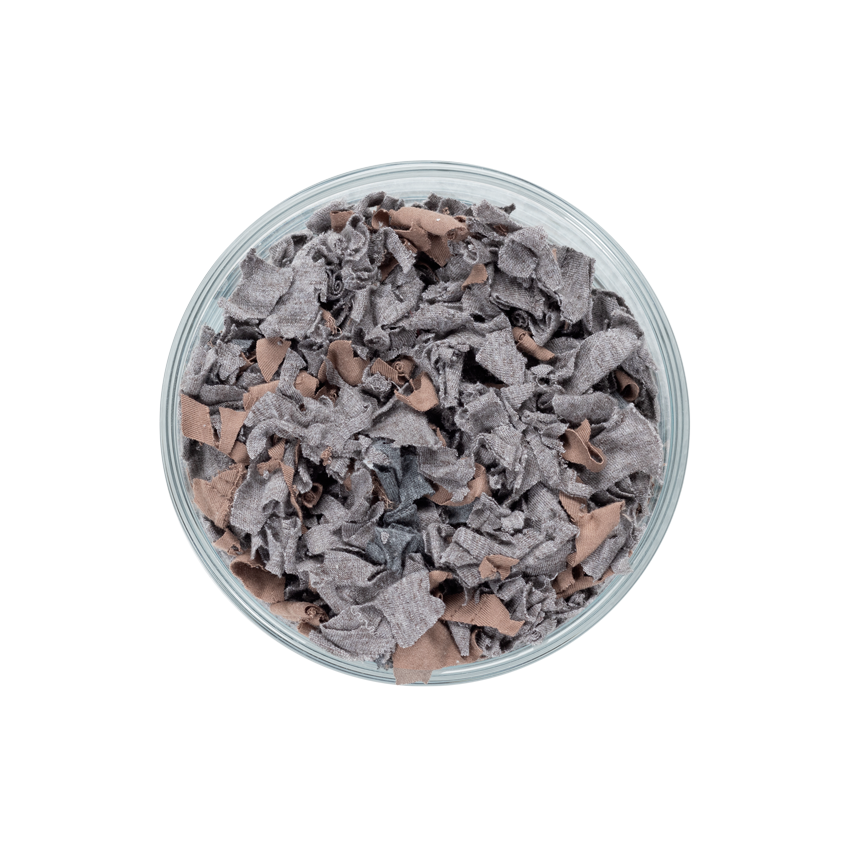
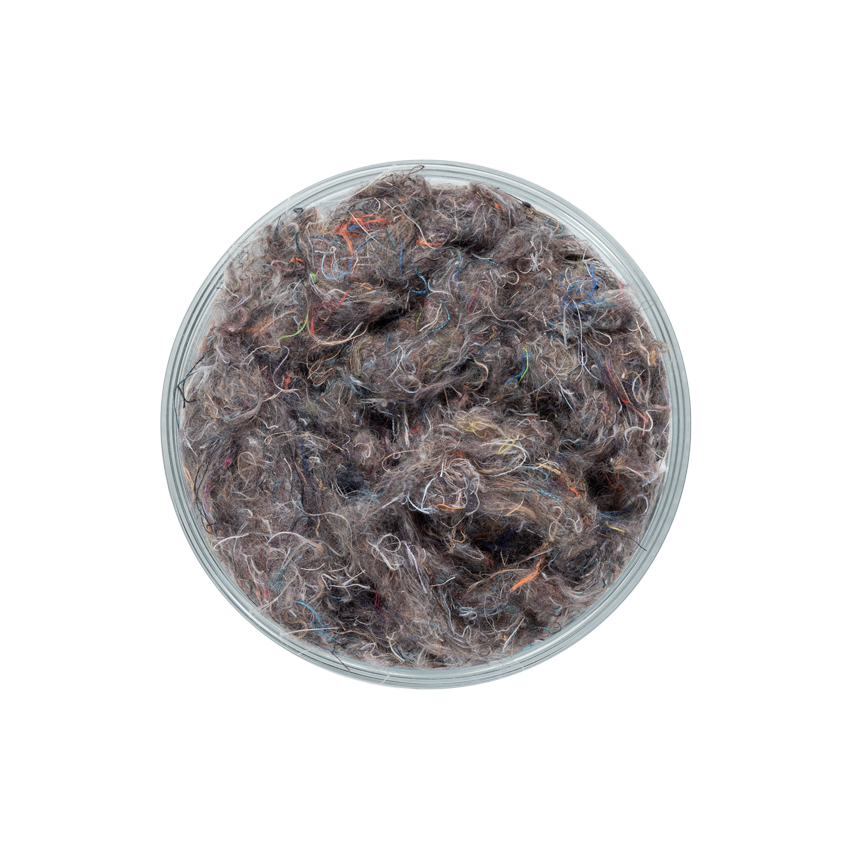
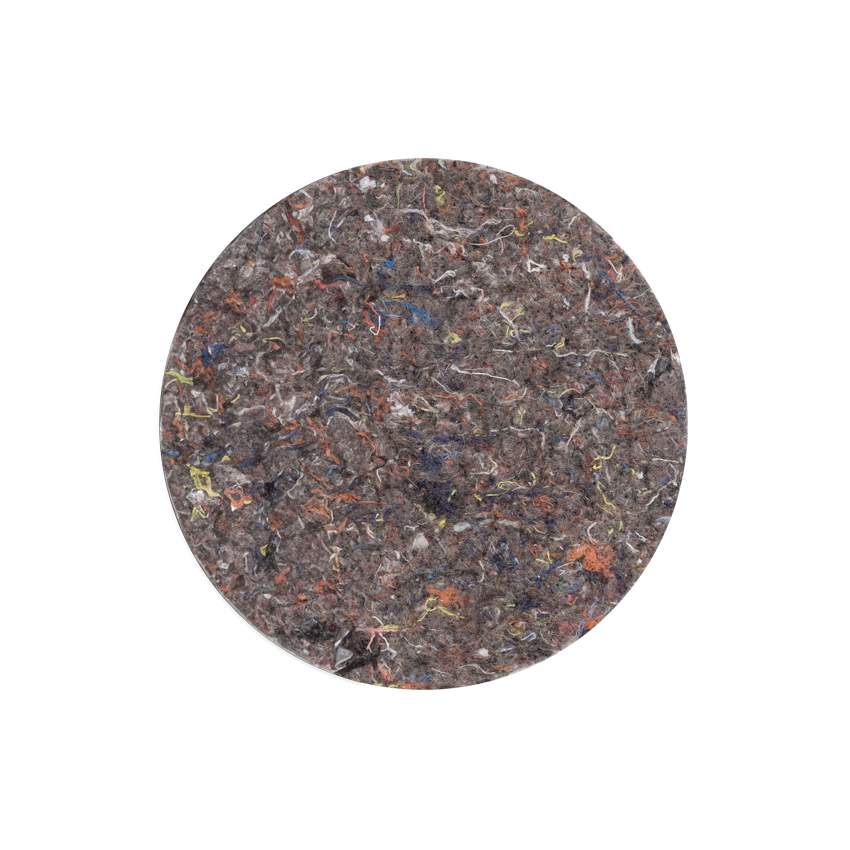
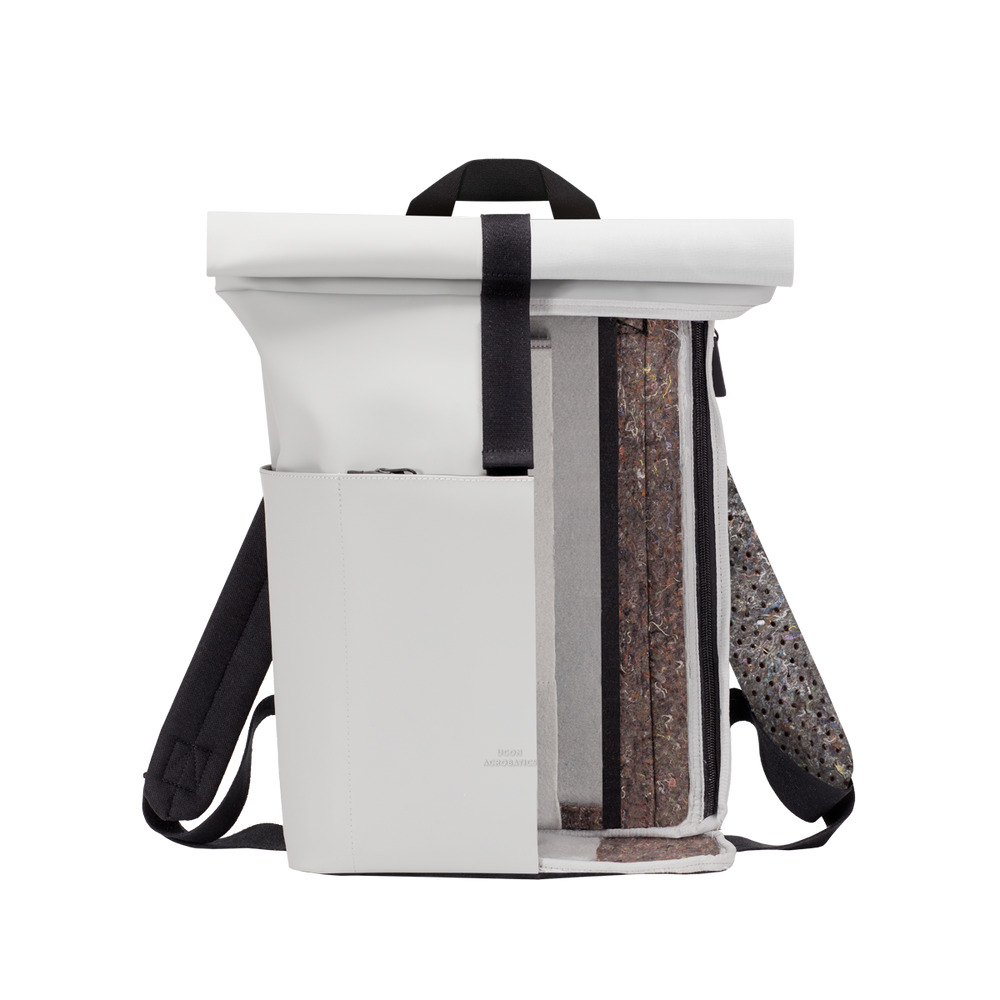
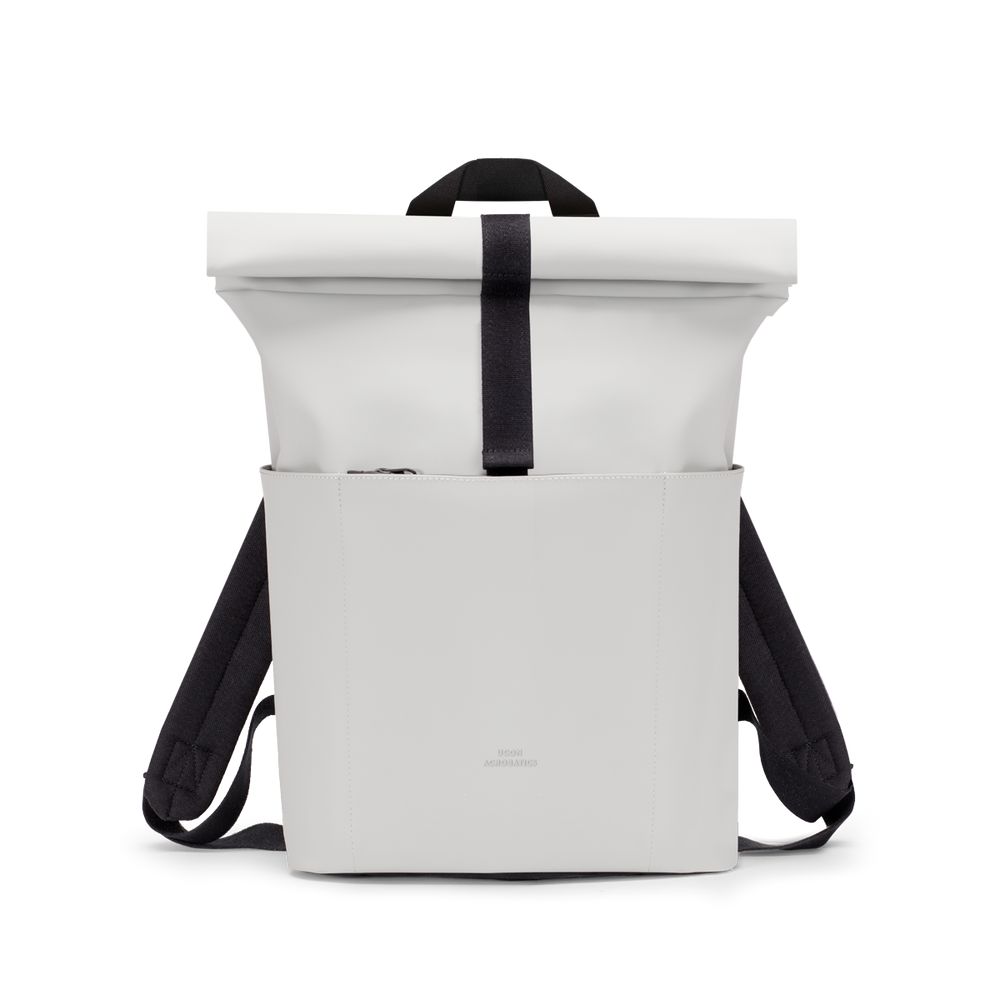


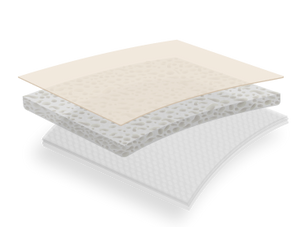
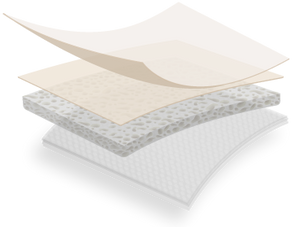
Lotus Infinity Material 'PUrTEX∞'


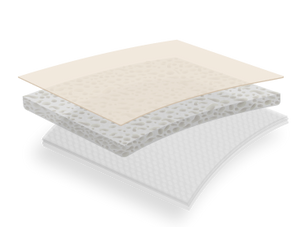
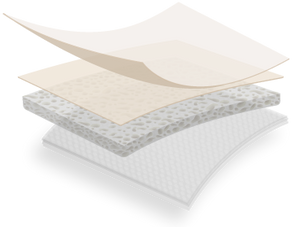
Tensile strength
Tear resistance
Adhesion resistance
Abrasion resistance
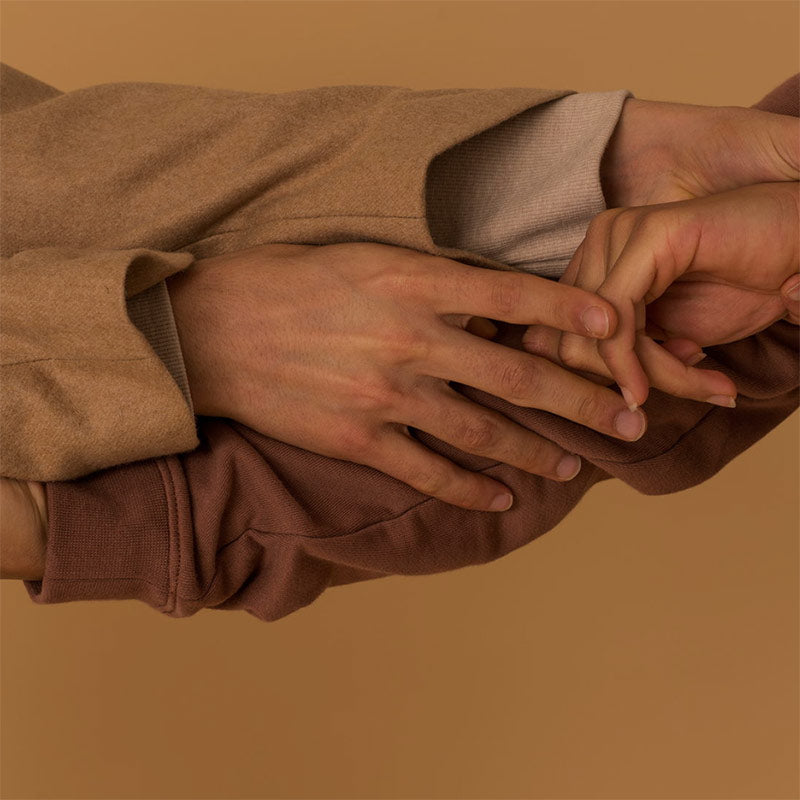

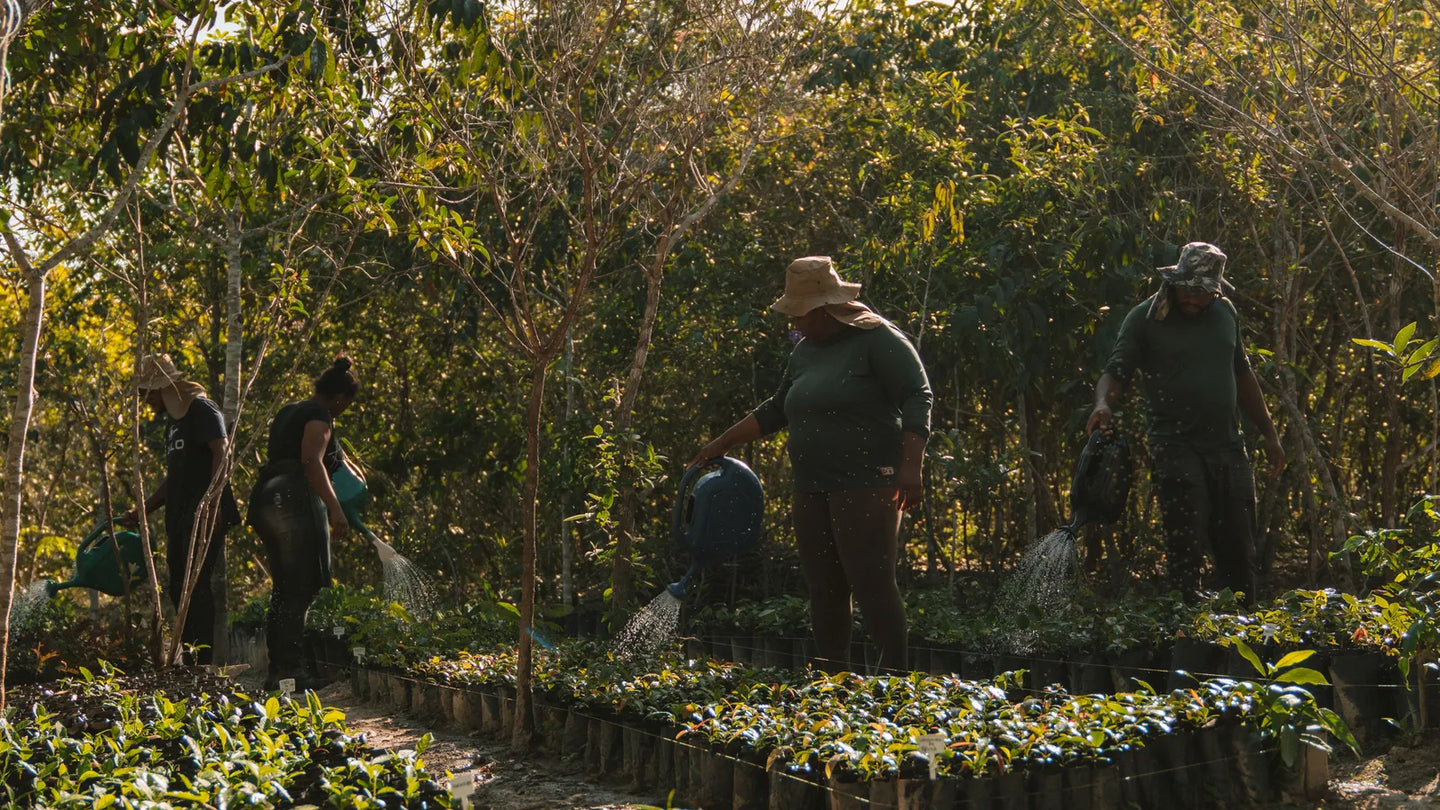
Ecologi
Together with our gold standard partner Ecologi we planted 25.000 trees in 2022 mainly through the 'Eden Reforestation Project'. With each purchased product in our online shop our customers help to plant one more tree and let our forest grow.

Plastic
Fischer
Our partner Plastic Fischer is a social enterprise that develops cost-efficient technologies to collect plastic waste from rivers before it can enter the oceans. With each purchased product in our online shop our customers help Plastic Fischer to remove 1kg of river plastic from rivers in Indonesia.